The Toyota Production System (TPS) Revealed
- andrewsalimu
- Dec 13, 2021
- 13 min read
Updated: Jan 28, 2022


Manufacturing is considered to be one of the most important activities for wealth creation in any economy. It is no wonder Japan has emerged as a major industrialized country starting from the mid - 20th century - and going on into the 21st century - owing to the success of the “Japanese Production System”, inspired by leading innovations and technologies based on great ideas and strategies. The “Japanese Production System” is commonly referred to as Lean Manufacturing and is the most successful system among the industrialized countries. Japanese manufacturers such as Honda, Nissan, Mazda, Mitsubishi, and Toyota have all come to adopt lean manufacturing over the years, meaning they only make cars according to customer requests. This, in turn, has significantly reduced waste from overproduction.
Starting from almost complete ruin after World War II, Toyota Motor Corporation rose to become the largest car maker in the world in mid-2000’s. This is largely because the company developed the Toyota Production System which has helped the company to become the most profitable car manufacturer in the world. As of September, 2021, Toyota Motor Corporation ranked 2nd in terms of Generated Revenue, after Volkswagen – followed by Daimler AG and Ford Motor Company, in that order. Currently, the company has its headquarters in Toyota City, Aichi, Japan. And the affiliated automotive brands of Toyota Motor corporation include Toyota, Lexus, Hino and Daihatsu.
Lean Manufacturing (Lean Management, or just “Lean”), has its roots in the Toyota Production System (TPS). The various tools, practices, methods, and techniques developed as part of the Toyota Production System have come to be collectively called “lean manufacturing” or simply just “lean”. Why lean? Because the Toyota Production System focuses on eliminating waste and doing just those things that deliver value a customer is willing to pay for. And that is consistent with the concept of lean.
The good news is: Principles of the Toyota Production system can be successfully applied in any type of organization and in any industry.
What is The Toyota Production System (TPS)?
The Toyota Production System (TPS) is an integrated socio-technical system developed by Toyota Motor Corporation to organize their manufacturing operations including logistics, supplier management, up to customer delivery. It is a way of making things that is sometimes referred to as a "lean manufacturing system," or a "Just-in-Time (JIT) system," and has come to be well known and studied worldwide.
Illustration of The TPS

Figure 2: Illustration of the Toyota Production System (Toyota Europe 2021)
What Concept is the TPS Based on?
The Toyota Production System (TPS) was established based on two concepts:
Jidoka: When a problem occurs, the equipment stops immediately, preventing defective products from being produced; and the
Just-in-Time: This is a concept in which each process produces only what is needed for the next process in a continuous flow.
The concepts of Jidoka and Just-in-Time, as they fit into the total Toyota Production System(TPS), are best illustrated by the ‘House of Toyota’ below:

Figure 3: House of Toyota (Lean Strategies International 2021)
Goals - These are represented by the Roof and include measurable outcomes such as Quality, Cost, Delivery Time, Environmental Performance and Safety Performance
Pillars - The two pillars represent the ‘just - in – time’ and Jidoka, the concepts on which the TPS is based. The just-in-time system ‘supports’ the idea that we should always deliver the right part, in the right amount at the right time. And Jidoka supports the quality in the system. Thus, together, quality and effective, efficient production provide the much needed support to the goals.
Foundation/Stability – Gives the strength and support to the pillars. This is made up of three elements: Heijunka, Kaizen and Standardization, i.e.:
Stability = Heijunka + Kaizen + Standardization
People/Culture -The Central part of the House of Toyota represents the “Thinking-People System” which includes: employees, customers and suppliers.
The House of Toyota helps one to visualize how competitive advantage can be gained through customer satisfaction:
· By increasing the level of Just-in-time and Jidoka
· Through engaging people into heijunka, standardized work and kaizen
· And resting on a basis of stability
Jidoka
The term jidoka used in the TPS (Toyota Production System) can be defined as ‘automation with a human touch.’
Jidoka/Autonomation - Intelligent Automation or Automation with a Human Touch – is one of the pillars of the TPS. This means that machinery will automatically detect an issue and safely stop so that an inspection and any necessary adjustments can be made. Information is shared with others on the “andon” display board and operators can continue working on other machines. This prevents production of defective products and eliminates over production. At Toyota, this is a four step process
1. Machine identifies the anomaly
2. Machine stops working
3. Fix/correct the anomaly
4. Identify the root cause and correct it.
For Toyota, jidoka means that a machine must come to a safe stop whenever an abnormality occurs. Achieving jidoka, therefore, requires building and improving systems by hand until they are reliable and safe. First, human engineers meticulously build each new line component by hand to exacting standards, then, through incremental kaizen (continuous improvement), steadily simplify its operations. Eventually, when any operator can use the line to produce the same result, the jidoka mechanism is incorporated into actual production lines.
Machines and robots cannot think or evolve on their own. Rather, they evolve as we transfer our skills and craftsmanship to them. Continuous improvement in both human skills and technologies is the essence of Toyota's jidoka.
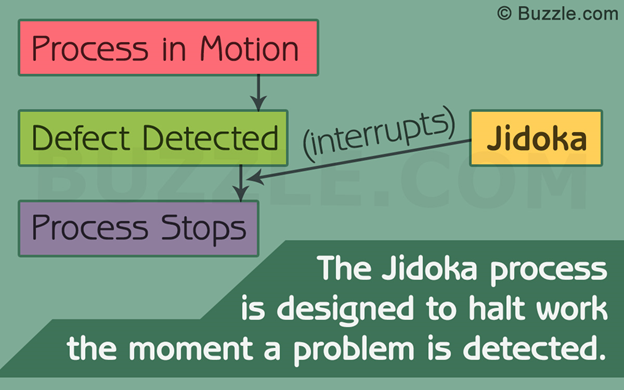
Figure 4: Illustration of the Jidoka principle (Business Zeal 2021)
Just-in-Time
Just-in-time implies making only what is needed, when it is needed, at every stage of production. This ensures there is no waste and that there is consistent quality and an even flow of production. The Kanban System is central to the success of the just-in-time process as it provides the means for automatic, real-time replenishment of parts at the line side in order to maintain minimal stock.
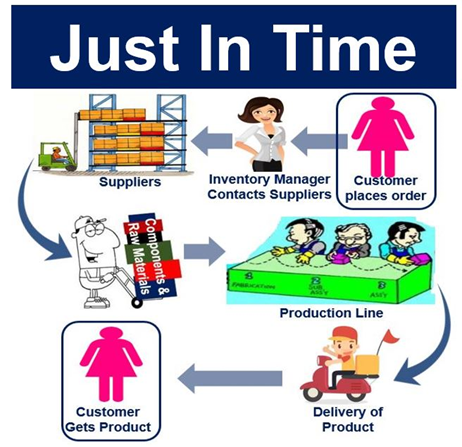
Figure 5: Illustration of Just-in-Time (Market Business News 2021)
In order to fulfill an order from a customer as quickly as possible, the vehicle is efficiently built within the shortest possible period of time by adhering to the following (Figure 2):
When a vehicle order is received, production instructions must be issued to the beginning of the vehicle production line as soon as possible.
The assembly line must be stocked with the required number of all necessary parts so that any kind of ordered vehicle can be assembled.
The assembly line must replace the parts used by retrieving the same number of parts from the parts-producing process (the preceding process).
The preceding process must be stocked with small numbers of all types of parts and produce only the numbers of parts that were retrieved by an operator from the next process.
Takt Time
Another important consideration for successful operation of “Just-in-Time” is Takt Time.
Takt time is a key element of lean manufacturing. In the Toyota Production System (TPS), the actual speed of the production line is balanced to exactly meet the demands of the customer. This speed or tempo of manufacturing, exactly matched to customer demand, is called takt time.
For a given product line, this pace is determined by dividing the allowable time in the production shift (for example eight hours, or 28,800 seconds) by the average production volume (for example 1000 cars).
Takt time, or the rate of production, for the day becomes 28.8 seconds. Work at each operation is planned to be as close as possible to the takt time. Anything faster is over-production and slower is under-production.
What are the Origins of The TPS?
The Toyota Production System was developed by Taiichi Ohno and Eiji Toyoda, Japanese industrial engineers, between 1948 and 1975, it preceded the more generic "lean manufacturing".
Jidoka - the oldest part of the TPS - was created in 1902 by Toyoda founder Sakichi Toyoda. It began when he invented a loom that automatically stopped whenever it detected that a thread was broken. This is the concept of building quality into the production process as well as enabling separation of man and machine for multi-process handling. The idea originated in the Toyoda Spinning and Weaving company which was started by Sakichi Toyoda. It was one way of preventing the process from producing defective products.
Later, in 1937, Kiichiro Toyota coined the phrase “Just-in-Time”, after the Toyota Motor Corporation was created. Kiichiro Toyoda believed that "the ideal conditions for making things are created when machines, facilities, and people work together to add value without generating any waste." He developed methodologies and techniques for eliminating waste between operations in processes which resulted in the Just-in-Time method.
Taiichi Ohno, an upcoming industrial engineer in the Toyoda Spinning and Weaving Corporation, was tasked with improving operational productivity and driving in the concepts of Just-In-Time and Jidoka when he was brought over to the Toyoda automotive business after World War II. He tried many concepts in production between the years 1945 and 1955, after he became in charge of the machine shop. And what is today widely acknowledged as the ‘Toyota Production System’ is largely the culmination of his work and effort during this time.
A catalogue of other tools and techniques were also developed at Toyota, including: 7 Wastes, Standardized Work, 5S, SMED, Visual Control, Error Proofing, as well as many others.
The Toyota spirit of Monozukuri (making things) is today referred to as the ‘Toyota Way’. It has been adopted not only by companies in Japan and within the automotive industry, but in production activities worldwide, and continues to evolve globally.
13 Pillars of The TPS
Kanban, Just-in-Time and Jidoka, plus ten other conceptual pillars, make up the Toyota Production System philosophy. Collectively, they are popularly known as the Thirteen Pillars of the Toyota Production System. And they are briefly defined as follows:
Kanban (English: Signboard)
A system that conveys information between processes and automatically orders parts as they are used up. Every item or box of items that flows through the production process carries its own kanban. Kanbans come off items that have been used or transported and go back to the preceding processes as orders for additional items.
Just-In-Time (JIT)
Just-In-Time production means only making what is needed, when it is needed and in the amount needed. TPS operates a “pull” system. When each vehicle is made to order, a signal is sent for parts to be replaced, thus maintaining the parts and materials inventory at a balanced level. Production and transport take place simultaneously throughout the production sequence.
Jidoka (English: automation with human intelligence)
It is the principle of designing equipment to stop automatically and to detect and call attention to problems immediately, whenever they occur.
Muda (English: Waste)
“Muda” refers to a wide range of non-value-adding activities. For example, anything an operator has to do within a process which does not add value but does add cost. Eliminating waste is at the heart of the Toyota Production System (or Just-in-Time).
Muri (English: Overburden)
Eliminating overburden of equipment and people is one of the main principles of the Just-In-Time system. Overburden can be avoided evenly distributing production in the assembly processes.
Mura (English: Unevenness or irregularity)
Eliminating unevenness or irregularities in the production process is key to the success of the Just-In-Time system, the main pillar of the Toyota Production System.
Genchi Genbutsu (English: Go and see for yourself)
The best practice is to go and see the location or process where the problem exists in order to solve the problem quickly and efficiently. To understand the problems, confirm the facts and analyze root causes.
Heijunka (English: Production smoothing)
A levelling technique to facilitate Just-In-Time (JIT) production and to smooth out production in all departments, as well as that of suppliers over a period of time.
Andon (English: ‘Sign’ or ‘Signal’)
‘Andon’ refers to visual aid which highlights where action is required (e.g the flashing light in manufacturing plants that indicate the line has been stopped by one of the operators due to some irregularity). This way, problems are highlighted in order to immediately apply remedies to prevent re-occurrence.
Kaizen (English: Continuous improvement)
‘Kaizen’ provides the means to ensure maximum quality, the elimination of waste, and improvements in efficiency. Kaizen activities include measures for improving equipment, as well as improving work procedures.
Konnyaku Stone
The ‘Konnyaku Stone’ is a small but important tool used in the Toyota Production System. It is used to smooth body panels before they are painted and to eradicate tiny imperfections. (Konnyaku stone is not really a stone at all – it is made of a mix of fine gritty resins.)
Poka-Yoke (English: Mistake-proofing)
Failsafe devices in the production process (sensors, templates etc.) that automatically stop the line when an abnormality occurs. This also ensures critical parts/components can only fit one way.
Hansei (English: Self-reflection)
Toyota recognizes the need for a hansei-kai, or reflection meeting (regardless of whether a task is easy or not). This process helps to identify failures experienced along the way and create clear plans for future efforts.
Nemawashi (English: Laying the groundwork or foundation)
The first step in the decision making process where the company seeks the opinion of employees about the decision.
The Toyota Production System became the basis upon which “Lean thinking and production” was founded. The lean Methodology was popularized by researchers from the Massachusetts Institute of Technology in the 1990s in a book titled: “The Machine that Changed the World”. Today, we see Lean being used across industries outside of manufacturing and enabling sustainable businesses all over the world.
Advantages of The TPS
The Toyota Production System offers many advantages over traditional/conventional mass-production systems when implemented as a means of improving the current production system. The following are some of the advantages:
The system enables continuous improvement by creating a culture that involves employees at all levels of the organization in discovering problems and solving them.
TPS improves quality in products and processes by employing lean techniques and methods such as: Kaizen, 5S, 5 Whys, and Poka-Yoke.
TPS applies the concepts of Just-In-Time (JIT), Kanban, Takt-Time, and Kaizen to spot and reduce waste, and to increase efficiency and reduce costs. The high-quality and cost-competitive products Toyota produces can be attributed to the fact that - throughout the production process - Toyota is able to constantly reduce the 7 wastes attributed to:
Wasted movement,
Waiting (wasting time)
Over -production,
Over-processing,
Inefficient transportation,
unnecessary inventory, and
Defects.
These wastes are identified and improved upon until they are eliminated.
4. TPS improves customer satisfaction by providing products that are free of defects. This is achieved through the zero-defect policy and continuous improvement, so that the company is able to deliver quality at a price customers can afford.
5. TPS improves all aspects of safety for employees and customers. It uses Lean tools and techniques to identify and eliminate hazards, and ultimately reduce risks.
What can you learn from the Toyota Way?
There are many valuable lessons that can be drawn from the Toyota Production System – or the Toyota Way, as it is often called – and its unparalleled success. Two schools of thought advanced by two different prominent Lean researchers, below, attempt to explain why the TPS is so successful.
A System to Continually Improve Work
Dr. Jeffrey Liker, a professor of industrial engineering at the University of Michigan, analyzed the philosophy and principles in his 2004 book, “The Toyota Way”. Liker characterizes the Toyota Way as "a system designed to provide the tools for people to continually improve their work."
According to Liker, Toyota's management philosophy can be broken into 14 guidelines categorized under four main principles:
Long-term philosophy: The focus should be on extended sustainability rather than short-term gain and fostering a sense of purpose in employees for productivity.
The right process will produce the right results: Continuous improvement is promoted by eliminating the seven wastes.
Add value to your organization by developing your people (employees, business partners and suppliers).
Continuously solve root problems to drive organizational learning: Managers must monitor operations personally to understand problems; solutions should be determined through consensus and implemented swiftly.
A Learning Organization
On the other hand, in his book, Managing People for Improvement, Adaptiveness and Superior Results (McGrawHill, 2009), Mike Rother links the quality of problem solving and learning at Toyota to the presence of a coach. He explains that this is the reason why Toyota is so much better than any other company at solving both detailed and strategic problems.
He adds that the firm has developed a unique approach explicitly based on learning, both at the detail and strategic levels. In particular, it has developed practices and processes to:
Contextualize learning by constantly insisting on genchi genbutsu: going to the real place to see the facts at their source.
Create learning labs in the day-to-day work environment. Toyota has developed a practice of structuring any working environment as a “learning lab” through its knowhow of visual management, instead of simulations.
Use the systemic nature of supply chain environments as a key to learning. By developing “pull systems,” Toyota has learned to link all steps of the chain in a smooth flow, along with the discipline to do so. Pull systems across the value stream act both as an architecture to improvement and as platforms for cross-functional problem solving.
Share knowledge. The practical understanding of systemic interactions in the company has led it to focus explicitly on knowledge sharing both up and down the line and across functions.
Constantly create knowledge, from detailed kaizen (continuous improvement) to radical innovation. This fundamental commitment to the scientific method of observation (genchi genbutsu), theory formulation (standards), focusing on anomalies (problems), experimenting (kaizen), measuring (check), and reformulating and generalizing (yokoten) is the engine of progress in the firm’s management approach.
Toyota’s problem solving does not occur in a vacuum, but under the guidance and control of a coach (Sensei) who makes sure the problem-solving process itself progresses with every cycle. The sensei is not a boss in any sense. He or she has no power and can only suggest, never tell. The sensei’s job is to help the manager develop his or her own lean thinking through practical hands-on exercises on the shop floor.
From the foregoing arguments, it can be concluded that Toyota is really a learning organization, in that the organization is skilled at creating, acquiring, and transferring knowledge, and at modifying its behavior to reflect new knowledge and insights.
It can also be safely concluded that the Toyota Production System (TPS) is more than just an integrated socio-technical system to organize and improve manufacturing operations, but also a vehicle to constantly improve both the technological and human aspects of the organization -in response to market demands - driven by organizational learning and problem solving.
Taiichi Ohno, in his 1988 book entitled: “Toyota Production System: Beyond Large-scale Production” stated:
“The Toyota production system, however, is not just a production system. I am
confident it will reveal its strength as a management system adapted to today's
era of global markets and high-level computerized information systems.”
References
Toyota Production System Basic Handbook. Art of Lean, Inc.
Toyota Production System. Available at: https://global.toyota/en/company [Accessed September 20th 2021]
Jidoka Process Explained with Examples. Available at: https://businesszeal.com [Accessed September 4th 2021]
Just-in-time: Meaning and Definition. Available at: Marketbusinessnews.com [Accessed September 5th 2021]
The House of Toyota. Available at: https://www.leanstrategiesinternational.com [Accessed September 25th 2021]
Toyota Production System. Available at: www.toyota-europe.com [Accessed September 10th 2021]
Toyota Way. Available at: https://whatis.techtarget.com [Accessed September 10th 2021]
Toyota Production System. Available at: https://kanbanzone.com/resources [Accessed September 4th 2021]
Toyota Production System. Available at: https://www.graphicproducts.com [Accessed September 7th 2021]
Toyota Production System Glossary. Available at: https://mag.toyota.co.uk [Accessed September 7th 2021]
Evolution of the Toyota Production System. Available at: https://eandt.theiet.org [Accessed September 27th 2021]
Autonomation vs Automation, Jidoka. Available at: https://www.benchmarksixsigma.com [Accessed September 30th 2021]
Rother, M. (2009). Toyota Kata: Managing People for Improvement, Adaptiveness and Superior Results. McGraw-Hill Education
Liker, J., K. (2004). The Toyota Way. McGraw-Hill Education
Ohno, T. (1988). Toyota Production System: Beyond Large-scale Production. Productivity, Inc., New York, NY 10016
This article will be very helpful to anyone who wants to lean about the Toyota Production System and lean, and to prepare for certification in the same.
You may contact me directly for any of the following reasons:
1. Comments on the article
2. General questions concerning the Toyota Production System (TPS)
3. Consultation in areas of Lean, TPS, Six Sigma and ISO 9001
4. ISO Corporate and Professional certifications.
About the Author
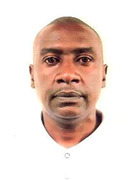
Andrew Salimu is an independent Consultant who works with organizations of all kinds to help them Improve their processes, improve productivity, and to implement ISO Standards. Andrew believes Process improvement and optimization are key for any organization to grow and remain profitable and competitive in today’s global economy. Andrew has various certifications, including Project Management, ISO Management Systems, Six Sigma, Lean, Digital Marketing, Strategic Management, Kaizen and Toyota Production System. He holds a BEng degree in Mechanical Engineering from The University of Birmingham, England.
E-mail: andrewsalimu@yahoo.com
Comments