The Digital Supply Chain in Industry 4.0
- andrewsalimu
- Sep 9, 2022
- 8 min read
Updated: Sep 28, 2022
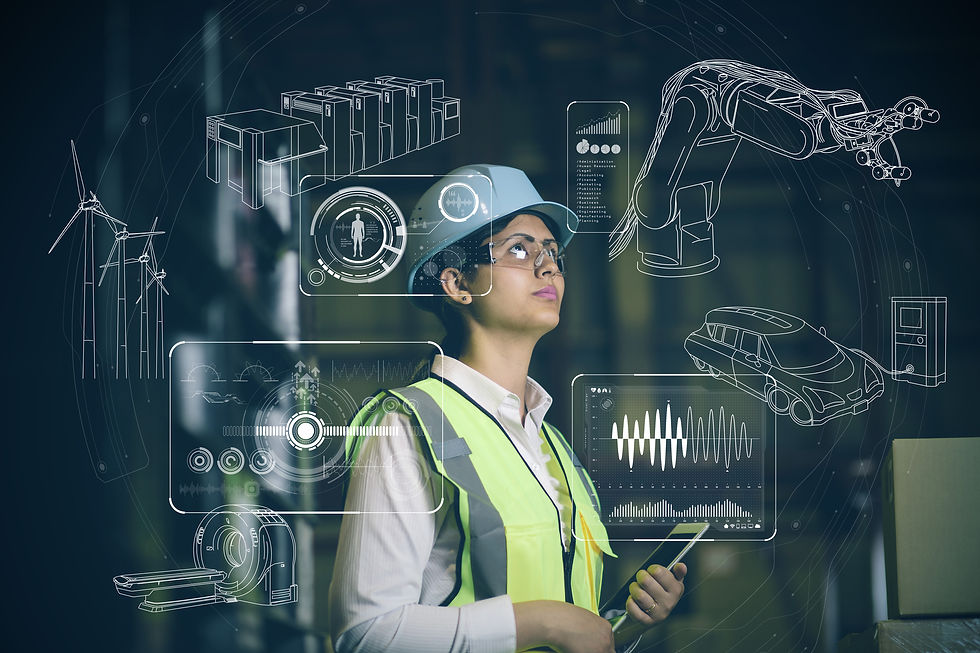
Introduction
Long before the onset of industry 4.0 in 2011, the desired characteristics of any supply chain were already widely known across all industries. These qualities include: resilience, responsiveness, agility, flexibility and transparency. The advents of Covid-19 and the Ukraine war have only served to reinforce what supply chain professionals had long known, that: “uncertainty is the only real certainty.” The current economic environment is posing many challenges to all kinds of organizations and businesses the world over. Organizations have to maintain stability in crucial supply chains and preserve the desired characteristics of these supply chains under very difficult circumstances. The obtaining highly uncertain and volatile situation, has brought about the need for organizations to constantly re-invent and be open to conducting business in new ways. And this is where technology has shown itself to be a game changer.
Sudden spiking or dropping of demand, supply disruptions, production line shutdowns - and many more such events - which are being experienced in most industries across the globe can only be managed by early prediction and real-time responsiveness. The implication of this is that businesses have to invest in a fair amount of state-of-the-art technology in order to remain competitive. Moreover, the ever-growing trend in automation and data exchange which has come with Industry 4.0 is exerting tremendous pressure on all players of supply chains to increasingly digitize and automate their operations.
What is Industry 4.0?
Industry has evolved significantly over the past centuries, and it is still evolving. The different stages of industrial development are commonly referred to as “revolutions." Figure 1 is a representation of the industrial revolutions.
The first industrial revolution ushered in mechanization, steam power and water power. Then followed the second industrial revolution, which brought about mass production and assembly lines that used electricity. The third industrial revolution gave birth to electronics, I.T. systems and automation. This was then followed by the fourth industrial revolution, which is associated with cyber physical systems.

Figure 1: Timeline of Industrial Revolutions
Industry 4.0 is a concept synonymous with the fourth industrial revolution (4IR) which relates to advancements of cyber-physical systems. It involves automation and data exchange in technology and processes within the manufacturing industry. This type of automation creates a manufacturing system in which all the devices and technology employed in production are wirelessly connected and use sensors and monitors to visualize entire processes. It also makes it possible to have a robust overview of a company’s manufacturing operations. Figure 2 illustrates how Industry 4.0 works.

Figure 2: Illustration of Industry 4.0 (twi-global.com 2022)
Industry 4.0 also includes areas that are not usually classified as industry applications in their own right, such as smart cities.
The technologies (and systems) at the core of industry 4.0 include the following:
Cyber-physical systems (CPS)
Smart manufacture
Smart factories
Cloud computing
Cognitive computing
Wireless connectivity and the augmentation of machines will be significantly enhanced with the full roll out of 5G. This will enable faster response times, allowing for near-real-time communication between systems.
Elements and Technology of the Digital Supply Chain
In simple terms, a digital supply chain is the application of electronic technologies to every aspect of the entire supply chain. It is a multi-faceted ecosystem linking product development, manufacturing and distribution networks into one fully transparent and digitized system.

Figure 3: Digital Supply Chain Illustration
This involves end-to-end digitization of the complete process, from suppliers, to manufacturing, to distribution, and to customers. Electronic sensors and tracking capabilities are integrated, enabling real-time monitoring of the movement of goods for end-to-end connectivity. As such, full transparency and visibility throughout each stage of the supply chain process is realized. Figure 3 represents a digital supply chain.
In digital supply chain management, process management and optimization are enhanced regardless of the complexity of the supply chain.
The digital supply chain consists, largely, of eight key elements:
Integrated planning and execution
logistics visibility
Procurement 4.0
Smart warehousing
Efficient spare parts management
Autonomous and B2C logistics
Prescriptive supply chain analytics, and
Digital supply chain enablers.
Companies that are able to piece together these elements into a coherent and fully transparent system will have a competitive edge in customer service, flexibility, efficiency, and cost reduction; whereas those that delay will lag behind.
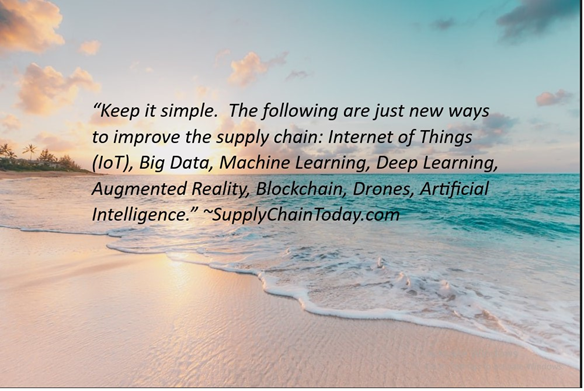
Electronic connectivity is at the heart of the Digital Supply Chain. Additionally, the technologies, systems and tools which support Digital supply chain are all in tandem with Industry 4.0 technologies, and they include:
The Internet of Things (IoT)
End to End Digital Connectivity
Cloud Computing
Big Data
Artificial Intelligence
Predictive Analytics
Virtual Reality
Augmented Reality
Voice Activated Technology
Wearable Devices
Control Towers
Robotics
3D Printing and On Demand
Additive Manufacturing
Cyber Security
Autonomous Vehicles
Drones
Software as a Service (SaaS), and many more.
Benefits of Digital Supply Chain
Generally speaking, digital automation can streamline processes, eliminate manual work, and reduce human error. Industry 4.0 technologies provide real-time, consistent, and accurate data to make more informed decisions. in times of supply crisis, deep insight into inventory and supply chain visibility are crucial. The use of applications and software that accurately predict possible bottlenecks helps supply chain managers to make quality decisions through predictive algorithms and other forms of data. Thus enabling them to find optimal ways to get products to the end market or customer. Figure 4, below, highlights the benefits of digital supply chain strategy with respect to Cost, Flexibility and Speed.

Figure 4: The Digital Supply Chain Strategy and its Benefits (A.T Kearny Analysis, 2019)
More specifically, the benefits of the digital supply chain may be summed up as follows:
Having better control over the supply chain: By making the right raw materials and production capacity available at the right time, efficiency increases.
Tendency to be More Forward-Moving: It enables the company to start thinking forward and becoming more forward-moving. Instead of focusing only on a backward-looking approach, adopting the opposite approach will increase the company efficiency and performance.
Ability to Connect and Relate Data Sources: The company is able to monitor real-time aspects of the different areas of the company and is thus able to improve processes, identify better ways to move products, and do preventive maintenance.
Using Data Visualization to generate Data-Driven Plans: Data visualization allows for one to see a clear representation of what is going on inside the various departments of the company. Analysis of this data, will help determine the areas of performance improvement.
Improved Collaboration: Data visualization allows one to make changes in both the physical and digital aspects of the supply chain. Ultimately, collaboration will improve.
Improved Cash Flow and Cost Management: Since the digital supply chain allows necessary adjustments to be made faster, minimal capital is tied up in the supply chain.
Happier Customers: The digital supply chain helps you to better understand what your customers need and want. And because you can afford to be flexible and agile in the digital supply chain, you can deliver exactly what your customers want and need faster, leaving them happier.
Challenges
There are numerous challenges that may arise for companies that are trying to fully digitize their operations in a bid to line up with the digital supply chain network. Among the common impediments are the following:
Large corporate organizations have a tendency to select an enterprise system for its core finance modules. Justifying a Supply Chain Digital Transformation system for other functions, like supply chain management, is often an afterthought.
Complex, intersecting processes on multiple legacy systems, with no single view, often cause supply chain complications in big companies.
Small companies may find that popular SaaS ERP platforms come with unexpected, additional costs, such as: connecters to Amazon, Walmart and eBay marketplaces and/or multi-jurisdiction tax calculators.
Supply chains are becoming increasingly complex, with global footprints, multiple selling channels and extreme levels of competition. In addition, the advent of unforeseen disruptors, like Amazon, introduces an entirely new urgency to the phrase “just-in-time.” This means that same-day or next-day delivery is now the norm.
Products are now becoming more segmented and differentiated, such that to meet the growing personalized customers’ expectations, company product lines have to be significantly increased. Supply chain execution is required to distinguish between the fast-moving purchases and the slower-moving products customers are willing to wait for.
The emerging hyper-focus to meet customer expectations is creating pressure upstream of the supply chain. Manufacturers need to extend visibility and collaboration beyond their own boundaries in order to curtail disruptions. To improve the entire network’s responsiveness and shorten lead times, trading partners have to collaborate more, so as to achieve a seamless product flow throughout the supply chain.
A study undertaken by PricewaterhouseCoopers (PwC) in 2016 highlighted the slow pace of digitization, and it stated in part: “… on the rise of Industry 4.0, only a third of companies surveyed have already started to digitize their supply chains, while 72% of respondents were not expecting to do so in the next five years.” [4]
The future
Resilience, Agility and Sustainability
The lessons learned from the Covid-19 pandemic and the ongoing conflict in Ukraine have changed the world’s perception of supply chain management from the standpoint of priorities. The new priorities identified as being critical to the management of the supply chain are resilience, agility and sustainability. If these priorities are properly addressed in the digital supply chain, the smooth flow of products in a complex, uncertain, and fast-changing environment will be assured.
The first of these new priorities, resilience, highlights the challenges that have made supply chain the prevalent topic of conversation.
The second, agility, pertains to the ability of companies to meet rapidly evolving, and increasingly volatile, consumer needs.
The third, sustainability, points to the pivotal role that supply chains are expected to play in the transition to a “green” and socially just economy.
According to a recent “Gartner analyst report”: When supply chain executives were asked “What technology adjustments is your company making, or planning to make, so as to achieve greater resilience or agility?” 66% stated they are investing in “Supply Chain Visibility and Mapping” and 58% are investing in “Enhanced Planning.” [3]

Figure 5: Shift in Supply Chain Strategy from Traditional to Next-normal (McKinsey & Company, 2022)
Figure 5 compares the areas of focus between Traditional supply chain strategy and Next-normal supply chain strategy.
Shift to Ecosystems
In a quest to overcome the shortcomings of the conventional approach to complex supply chains, supply chain managers are tending to adopt the Supplier ecosystem approach. In a supplier ecosystem, suppliers have more autonomy and supplier-supplier relationships are allowed to emerge. While the traditional approach leads to long, dispersed supply chains, the ecosystem approach focuses on tightening and integrating supply chains. The ecosystem approach highlights supplier autonomy while acknowledging the buying company’s leadership. Digital supply ecosystems lay emphasis on the following aspects:
Shared Data and Insights: Sharing information, trending data, and knowledge can benefit all ecosystem players. This will not only impact supply chains but also consumption trends in product categories such as foods and beverages.
Shared Applications: Sharing applications permit faster response and information flow through the entire ecosystem on consumer experience, volumes of product sold, and feedback on the entire experience. This, in turn, allows for rapid data based innovation of products, processes and services.
Shared Operations & Expertise: Ensuring that the product or service is available is critical to the success of the digital ecosystem. For this reason, sharing operations to ensure customer satisfaction will be key. Shared operations and expertise are critical for enabling a company to be resilient and flexible in meeting market demands and solving problems.
Conclusion
Industry 4.0 has helped to convert supply chain management to digital supply chain management. To form a clear picture of the future digital supply chain, we have to recognize that an evolution of supply chain systems is taking place, from fully owned and vertically integrated systems to industry ecosystems of partners, data, and experiences. Key to the success of the ecosystem are speed, transparency, and flexibility across a portfolio of physical and digital (software) products and services. It is now widely accepted that whatever form future digital supply chains may take, they will need to be more resilient, agile and sustainable, so that they can meet ever-growing market demands in an increasingly volatile and uncertain business environment, while promoting a “green” and socially just economy.
References
https://logisym.org/using-technology-to-build-sustainable-supply-chains/
https://cargonow.world/employing-digital-logistics-platforms-to-achieve-supply-chain-sustainability/
https://cargonow.world/gartner-research-3-trends-shaping-future-supply-chains/
https://logisym.org/profitable-agility-and-resilience-in-supply-chain-execution/
https://logisym.org/innovations-in-using-technology-to-stay-ahead-in-the-game/
https://www.alsioman.com/industry-4-0-supply-chain-management/
https://logisym.org/wp-content/uploads/2021/07/LGSM_JUNE_JULY_2021.pdf
https://cargonow.world/the-hard-economics-of-justifying-a-supply-chain-digital-transformation/
https://logisym.org/optimising-supply-chain-management-in-industry-4-0/
https://www.strategyand.pwc.com/gx/en/insights/2016/industry-4-digitization/industry40.pdf
https://supplychaindigital.com/digital-supply-chain/what-does-industry-40-mean-supply-chain-network
https://www.mckinsey.com/business-functions/operations/our-insights/future-proofing-the-supply-chain
https://www.plex.com/products/analytics-and-industrial-iot/what-is-industry-4-0
About the Author
Andrew Salimu is an independent Consultant who works with organizations of all kinds to help them improve their processes and productivity, and to implement ISO Standards.
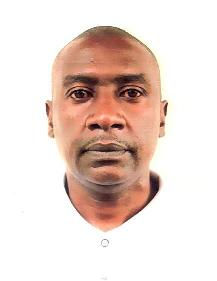
Andrew believes Process improvement and optimization are key for any organization to grow and remain profitable and competitive in today’s global economy.
Andrew has various certifications, including Project Management, ISO Management Systems, Six Sigma, Lean, Digital Marketing, Strategic Management, Kaizen and Toyota Production System. He holds a BEng degree in Mechanical Engineering from The University of Birmingham, England.
LinkedIn: https://www.linkedin.com/in/andrew-salimu-33562b6a/ Website: https://andrewsalimu.wixsite.com/website
E-mail: andrewsalimu@yahoo.com
Comentários