Six Sigma Made Easy
- andrewsalimu
- Dec 11, 2021
- 12 min read
Updated: Jun 23, 2022

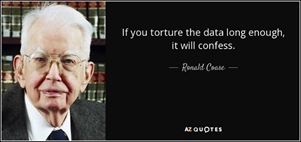
Whether you want to improve a manufacturing process, to reduce the time of pizza home deliveries, to reduce the time spent on queues in a super market, or, indeed, to make scheduling of operations on patients in a hospital more efficient, the challenges you face have something in common. You are trying to improve customer satisfaction, and to make the processes more efficient and cost effective. And, of course, at the same time you are striving to keep the bottom line of the organization within budget.
The advent of globalization, technological advancements, legal requirements and increasing customer demands – among other things – have not made it any easier to run businesses of all sizes and types all over the world. As such, business leaders and managers are constantly looking for ways to keep up with the ever-growing demands of business in order to grow their enterprises or, let alone, keep them afloat. To this end, organizations have, over the years, developed a plethora of quality management programs and business-process improvement programs, most of which have only achieved limited, incremental success in the face of the ever-changing – and growing- business challenges.
It is against this backdrop that engineers at Motorola (USA) in the mid to late 1980’s developed the methodology of Six Sigma. At, the time the company was plagued with serious quality problems. The success of Six Sigma at Motorola was so unprecedented that it, almost immediately, encouraged many other organizations in the USA, and the world over, to start their own Six Sigma programs. The methodology owes its success to the fact that, when properly implemented, Six Sigma can bring about breakthrough improvement, i.e. improvement of 70% or more in quality, cost, delivery and efficiency in any process and industry. Furthermore, because Six Sigma process-improvement projects are carefully documented, they can be easily repeated.
What is Six Sigma?
Six Sigma is a methodology that applies a structured, scientific method to improve any aspect of business, organization or process. It is centered around disciplined data collection and analysis to determine the best ways of meeting customers’ needs while satisfying the needs of the organization, minimizing waste of resources and maximizing profit in the process.
Some details about Six Sigma
A Six Sigma performance is achieved when a process produces fewer than 3.4 defects per million opportunities of producing defects
A Six Sigma improvement is when the key results of a business or process are dramatically improved, typically by 70% or more.
A Six Sigma deployment is a planned, organization-wide implementation of the Six Sigma methodology.
A Six Sigma organization uses Six Sigma techniques and tools to achieve improvements in performance in areas such as: cost, customer satisfaction, revenue, process capacity and capability, cycle time; and reduction of errors and defects.
The Beginning of Six Sigma
The concept of Six Sigma was started by Bill Smith and Mikel Harry, both of Motorola. The then CEO of Motorola, Bob Gavin was persuaded by the dual to launch “The Six Sigma Quality Program” in 1987. This program helped Motorola to be the first company to receive the prestigious Malcolm Baldrige National Quality Award in the year 1988. And on December 28, 1993, Motorola registered Six Sigma as a trademark.
Inspired by the success at Motorola, a number of companies soon started implementing their own Six Sigma programs, and among them were General Electric, Allied Signal, Whirlpool, Honeywell, Dow Chemical and DuPont. By the late 1990s, roughly two-thirds of the Fortune 500 organizations looking to reduce costs, improve quality and improve customer satisfaction had adopted Six Sigma.
In 2011, the International Organization for Standardization (ISO) published the first standard "ISO 13053:2011" which describes Six Sigma as a methodology for business improvement, typically comprising five phases: define, measure, analyze, improve and control (DMAIC). The standard also recommends how Six Sigma projects should be managed and describes the roles, expertise and training of the personnel involved in such projects. It can be applied to manufacturing, service and transactional processes by any organization.
8 Key Principles of Six Sigma
The following are the main principles that govern Six Sigma:
Customer focus – their needs and expectations
Understand the flow of work – steps and their sequence in a process.
Create the value stream and identify and eliminate non-value adding processes
Ensure smooth processes flow.
Ensure all your methods are systematic and scientific
Eliminate defects by reducing variation.
Get buy-in from all key players
Create a robust, responsive environment
Six Sigma, Normal Distribution and Standard Deviation(σ) Explained
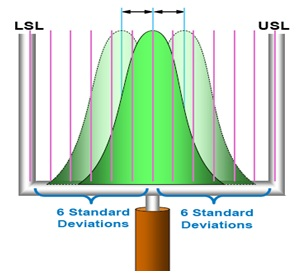
Figure 1: Six Sigma stands for 6 standard deviations (6σ) between average and acceptable limits (Six Sigma Institute™ 2021)
LSL and USL stand for “Lower Specification Limit” and “Upper Specification Limit”, respectively. Specification Limits are derived from the customer requirements, and they specify the minimum and maximum acceptable limits of a process, as illustrated in Figure 1.
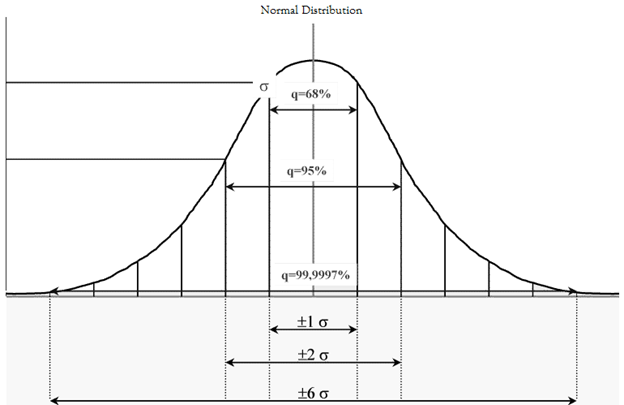
Figure 2: Normal Distribution (Vivekananthamoorthy N and Sankar S 2011)
Refer to Figure 2, for the following bullet points which together explain Six Sigma, Normal Distribution and Standard Deviation
Standard deviation (σ) is the average distribution of variation within a data set. It is how spread out individual data points are.
In the instance of Six Sigma, standard deviation relates to data that can be expressed as fitting a normal distribution. A normal distribution curve, sometimes known as a “bell curve,” is a plot of data where the three key measures of central tendency are all in the graph’s center. These three key measures of central tendency are as follows:
Mean – Arithmetical mean or calculated average.Median – The “middle value” or the value that falls in the center of the data when it is ordered.
Mode – The most commonly occurring value.
Six sigma is a statistical term, taken from the Greek Alphabet and denotes the measure of variation in a process output (Product).
The name, “Six Sigma (6σ)”, comes from the area under the normal distribution curve, after moving six standard deviations away from the center in each direction.
One of the characteristics of this distribution is that 68% of area (i.e. the data points) falls within the area of -1σ and +1σ on either side of the mean. Similarly, 2σ on either side will cover approximately 95.5% area. 3σ on either side from mean covers almost 99.7% area. This can be summarized as follows:
If the target is reached:
68% of the time, the process is operating at +/- 1 Sigma
95.5% of the time, they are operating at +/-2 Sigma
99.73 % of the time, the process is at +/-3 Sigma
99.9997 % of the time, the process is operating at +/-6 Sigma
Ideally, for a Six Sigma process, the specification limits (USL and LSL) should be 12 standard deviations apart (6 standard deviations on either side of the mean). However, standard "Six Sigma" methodologies allow a 1.5 standard deviation shift, so the mean could be 4.5 sigma from one specification limit, and 7.5 sigma from the other.
Sigma, the value of the standard deviation, refers to the extent to which variation can be allowed in a process without causing errors which make the process output (product) unacceptable with respect to specification limits.
It signifies the spread of the process output; so that the closer the spread, the lower is the standard deviation and higher the sigma rating, which indicates higher process capability.
The sigma value of the process is translated into standard measures of process capability, Cpk. The value of Cpk is 2.0 for a Six Sigma process, and between 1.0 and 1.33 for a normal Three Sigma process.
Six Sigma Methodologies (DMAIC & DMADV)
The two main methodologies employed in Six Sigma are DMAIC (Define, Measure, Analyze, Improve, Control) and DMADV (Define, Measure, Analyze, Design, Verify).
The DMAIC methodology is used when a product or process is in existence in an organization, but is not meeting customer specification or is not performing adequately. It addresses the current process and includes controls to sustain the gains.
DMADV is a Design for Six Sigma (DFSS) method that puts the focus on customers, and creating the right product or process correctly the first time. The methodology is used when:
A product or process is not in existence in the organization and one needs to be developed.
The existing product or process exists and has been optimized (whether using DMAIC or another methodology) and still does not meet the level of customer specification or Six Sigma level.
DMADV prevents defects and is part of the solution design process.
DMAIC (Define, Measure, Analyze, Improve, Control)
Define the faulty process and outline the problem, goals, and deliverables for the project that will help improve the process. The goals and deliverables should align with the enterprise strategy and customer needs.
Measure the initial performance of the process and collect data that is relevant to that. These statistical measures make up a list of potential causes of the problem and help the team understand the baseline performance of the process.
Analyze the data that has been accumulated and then verify it. The analysis involves isolating each input, or potential cause for the failure, and testing it as the potential root cause of the problem. Through analysis, the team identifies the root cause(s) of process variation.
Improve system performance by implementing solutions from the alternatives derived after analysis.
Control the process to ensure that the improvements are retained. Establish the process, set up control mechanisms and monitor the entire process.
DMADV (Define, Measure, Analyze, Design, Verify)
Define the goals that meet the demands of customers, and that align with the enterprise strategy.
Measure the product or service characteristics that are Critical To Quality (CTQ’s), production and risks. In this step, customer needs are used to create a specification which defines the product or service in a way that is measurable, so that data is collected and compared with the specified requirements.
Analyze and study the proposed process or product to determine whether there are better ways to achieve the desired results. A prototype may be built and analyzed at this stage. This step ensures that alternatives are developed, analyzed and incorporated in order to improve the process or product.
Design the new process or product, optimize it and plan for its verification. Simulations may be employed in this phase. For any revisions in design, the analysis step is repeated in order to compare the new design with the specified characteristics.
Verify the design to ascertain that the end result meets or exceeds the customer's requirements. The verification stage involves setting up pilot runs, implementing the process and handing it over to the process owners.
Six Sigma Techniques & Tools
Six Sigma methodology makes use of many powerful tools in continuous improvement projects and programs. The tools are broadly classified as:
1. Process Optimization and
2. Statistical Analysis tools.
Process Optimization tools allow one to design, simulate and optimize processes of work. They help to visualize how work is performed and identify where the source of the problem is. These include:
SIPOC (Suppliers-Inputs-Process-Outputs-Customers)
CT (Critical to) tree: Helps to identify, organize and display process parts according to areas of importance.
Modelling: Enables you to define and design Processes including flow, timing, resources, inspection, delivery etc.
Simulation: Makes possible the simulation of flow of work and materials in a process
Cause-and-Effect Matrix (C&E): Helps to determine significant contributors to the output.
Fishbone Diagram: It enables creation of a high level C & E with categories for each contributor.
FMEA (failure mode effects analysis): It defines potential failure modes, likelihood of occurrence and ability to detect effects of failure.
On the other hand, the purpose of Statistical Analysis tools is to analyze data collected from the real-world performance of a product or process. The aim is to turn data into knowledge so that one can make informed decisions.
These tools include the following:
Basic Stats
Plots and Charts
Time series
ANOVA (analysis of variance)
Design of experiments
Process Capability Analysis
Additionally, there are many useful qualitative and quantitative Six Sigma techniques that form part of the Six Sigma toolbox. And the key techniques that are most commonly used during a Six Sigma project include:
Brainstorming
Voice of the Customer
Root Cause Analysis (5 Whys)
The 5s System
Poka-Yoke/Mistake Proofing
Value Stream Mapping
What is Lean Six Sigma?
More recently, some practitioners have combined Six Sigma ideas with lean manufacturing resulting in a methodology called “Lean Six Sigma”.
Lean Six Sigma is the integration of Lean and Six Sigma tools and techniques aimed at producing the best possible quality, cost, delivery, cycle time and other process attributes.
Lean focuses on reducing waste and attains its goals through less technical tools such as 5S, Kaizen, Value Stream Mapping and Kanban.
Whereas Six Sigma is concentrates on reducing variation in the process and uses more of measurements, data collection and analysis, design of experiments and hypothesis tests.
There is no clear distinction between the two disciplines. Thus the term "lean Six Sigma" is being used more and more often, as process improvement requires aspects of both approaches to attain the best possible results.
Very often, successful implementations of Lean Six Sigma start with the application of Lean tools, making the workplace as efficient and effective as possible and reducing waste. More technical Six Sigma statistical tools may then be applied to clear the process problems that may persist.
Implementation of Six Sigma
Six Sigma may be implemented in an organization through one of the following methods:
1. As a Program or Initiative
This is where selected employees are taught six sigma tools from time to time and asked to apply them when required on their jobs. But because the initiatives may come from low levels of an organization, and because they may not align well with the strategic goals of the organization, they may face resistance from other employees within the organization that are affected by the same initiatives. While successes within an organization might occur under this implementation method, they do not build upon each other to encourage additional and better use of the tools and overall methodology.
2. As a Business Strategy Through Projects
Deploying Six Sigma through projects that are in line with business strategy is a more effective route. This is because Six Sigma practitioners are encouraged to apply their newly acquired training on predetermined projects, using the right tools at an appropriate time. In this way, more benefits are realized from the time and training spent on Six Sigma training.
Regardless of which of one of the above implementation routes is chosen, the following measures must be considered:
All members of the organization must be informed about the Six Sigma implementation, and trained where necessary. And a system must be put in place to recognize employees’ contribution to the Six Sigma efforts.
One person (ideally a Lean Six Sigma Black Belt or Master Black Belt) should be put in charge (of the implementation as a whole) and supported by a team of Six Sigma Green Belts in various departments of the organization.
A suitable Measurement System must be put in place for each aspect of the organization and process. Correct measurements and their records are critical to the success of any Six Sigma project.
Resources required for the project(s) must be put in place prior to commencement of the project(s).
Six Sigma Certification Levels and Roles
Six Sigma Practitioners have varying degrees of skill. The “Belt” system used in various industries to classify the Six Sigma skills is widely understood although not entirely universally accepted. The levels relate to specified training requirements, education criteria, job standards, and eligibility. And they are as follows:
White Belt
This is the lowest belt, where the newcomer is expected to participate in problem-solving projects and understand basic Six Sigma concepts.
Yellow Belt
In essence all other people in the organization who can apply Six Sigma methodology and improve their environment. They can assist Black Belts and Green Belts to complete projects. Yellow belts do not have to have the training, knowledge and skills of Black Belts and Green Belts, but they can assist in:
Carrying out measurements
Collecting data
Characterizing a process
Defining critical process factors
Make easy improvements
Cultivate improvement opportunities.
Green Belt
Green Belts are trained to solve the majority of process problems in both transactional and manufacturing environments. They must have a minimum of three years of full-time employment, and are made up of process owners, process leaders, operational staff, professional specialists, managers and executives. They understand the tools and methodologies used for problem-solving and have hands-on experience on projects involving some level of business transformation. Green Belts work under guidance of Black Belts and can lead Green Belt projects or teams on specific processes.
Black Belt
Black Belts are the most highly trained professionals in the complete set of Six Sigma techniques and tools. They require a minimum of three years of full-time employment and must have proof of completion of a minimum of two Six Sigma projects. Typically, Black belts:
Lead complex process improvement projects across departments, functions and business units that require significant amounts of data and high levels of analysis.
Mentor others in the application of Six Sigma techniques and tools
They conduct training, workshops, case studies, and the like, concerning application of new strategies and tools
Discover opportunities for new Six Sigma projects
Must demonstrate expertise at applying multivariate metrics to diverse business change settings
Master Black Belt
Master Black Belts (MBB) are hands-on experts who teach and mentor Black Belts, Green Belts and Yellow Belts. They must be in possession of a Black Belt certification and have a minimum of five years of full-time employment, or Proof of completion of a minimum of 10 Six Sigma projects. MBBs typically perform the following functions:
Own the Six Sigma curricula and Six Sigma knowledge content of their organizations
Develop key metrics and strategies.
Consult other belts on important business issues and specific project issues.
What are the Benefits of Six Sigma?
The following are the major benefits of Six Sigma:
1. Improved Time Management.
2. Increased Employee Motivation.
3. Higher Profits and Revenues, and Lower Costs.
4. Increased productivity
5. Reduced cycle time
6. Improved quality
7. Higher customer satisfaction
8. Improved communication among team members
9. Promotes Nimbleness
Career Opportunities in Six Sigma
Because of its wide application, Six Sigma finds use in almost all industries and work settings. As such, Six Sigma practitioners are routinely sort after by many reputable organizations of all kinds, especially Fortune 500 companies. Six Sigma levels normally match salary prospects.
Some of the common titles of Jobs for Six Sigma practitioners are as follows (although the precise nomenclature can vary from company to company):
Six Sigma Analyst
Six Sigma Black Belt
Lean Six Sigma Consultant.
Six Sigma Consultant
Director of Operational Excellence
Lead Manufacturing Engineer
Functional Project Lead
Process Development Engineer
Senior Project Manager
Six Sigma Projects Manager
Operating System Specialist
Business Process Manager
Lead Analyst/Project Manager
Warehouse Operations Manager
The list is not, by any means, exhaustive.
References
International Six Sigma Institute™. What is Sigma and Why is it Six Sigma. Available at: http:// www.sixsigma-institute.org [Accessed July 20th 2021].
Pankaj, K. (2021). What is Six Sigma: Everything You Need to know About it. Available at: http:// https://www.simplilearn.com
Vivekananthamoorthy N and Sankar S (July 14th 2011). Lean Six Sigma, Six Sigma Projects and Personal Experiences, Abdurrahman Coskun, IntechOpen, DOI: 10.5772/17288. Available at: https://www.intechopen.com/books/six-sigma-projects-and-personal-experiences/lean-six-sigma
ASQ. Title What Is Six Sigma. Available at: https://asq.org/quality-resources/six-sigma [Accessed July 24th 2021].
Mandal, S. K 2007, Fundamentals of Business, 2nd edn, Saurabh Printers Pvt.Ltd., Noida
Gygi, C., DeCarlo, N., & Williams, B. (2005). Six Sigma for Dummies. Wiley Publishing, Inc., Hoboken
Ronald Coase 2021, digital photograph, AZ Quotes, accessed July 27th 2021, <https://www.azquotes.com/author/30517-Ronald_Coase>.
This article will be very helpful to anyone who wants to refresh their knowledge in Six Sigma, to prepare for Six Sigma professional certification, to train employees; and even to gain foundational knowledge in Six Sigma.
You may contact me directly for any of the following reasons:
1. Comments on the article
2. General questions concerning Six Sigma
3. Consultation
4. Six Sigma, ISO Standards and Lean Online Professional Training
About the Author
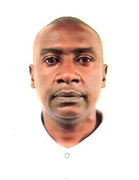
Andrew Salimu is an independent Consultant who works with organizations of all kinds to help them Improve their processes, improve productivity, and to implement ISO Standards. Andrew believes Process improvement and optimization are key for any organization to grow and remain profitable and competitive in today’s global economy. Andrew has various certifications, including Project Management, ISO Management Systems, Six Sigma, Lean, Digital Marketing, Strategic Management, Kaizen and Toyota Production System. He holds a BEng degree in Mechanical Engineering from The University of Birmingham, England.
E-mail: andrewsalimu@yahoo.com
Comments